What is a Fulfillment Center?
If you’re curious about a fulfillment center, you’ve come to the right place! A fulfillment center is a warehouse where online retailers store and process inventory for shipping to customers. It’s important to note that fulfillment centers are not the same as distribution centers, which are used to receive and store inventory from manufacturers.
When a customer places an order on an online store, the fulfillment center closest to them is notified. Warehouse staff then locate the inventory, pick it, pack it, and label it for shipment to the customer. This process, called order fulfillment, takes place entirely within the fulfillment center.
Fulfillment centers are crucial to the ecommerce industry because they allow online retailers to outsource the time-consuming and complex process of inventory management and order fulfillment. By using a fulfillment center, online retailers can focus on other aspects of their business, such as marketing and customer service.
Overall, a fulfillment center is a warehouse space where online retailers store and process inventory for shipping to customers. It’s an essential part of the ecommerce industry, and without it, online shopping as we know it would not be possible!
The Basics of Warehousing
Warehousing, while typically viewed as a storage solution, is a critical element of any supply chain, encompassing a variety of activities that enable businesses to efficiently store and manage their products. Here are some of the essential activities involved in warehousing:
- Receiving: This involves accepting products into the warehouse, as well as verifying their condition and quantity. Receiving personnel use inventory management systems and barcode scanners to validate and record the product’s receipt.
- Storage: After products are received, they are stored until they are needed. A well-designed warehouse layout is crucial to optimize space and ensure that products can be easily found and retrieved.
- Order Picking: This involves retrieving products from storage to fulfill customer orders. Order picking is typically done using handheld devices that direct warehouse personnel to the exact location of the products.
- Packing: Once products are picked, they are packed, and shipping labels are attached. The packaging process guarantees that products are protected during transportation and arrive at the customer’s location in good condition.
- Shipping: Once the packing process is complete, products are dispatched to customers using various shipping methods. Shipping is a critical component of warehousing, and businesses must guarantee that products are delivered on time and in excellent condition.
- Inventory Management: Warehouses must manage product inventory to ensure that products are available when needed. Inventory management involves monitoring the location and quantity of products and determining when to reorder products to maintain adequate stock levels.
What Are the Differences Between Fulfillment Centers and Warehouses?
When it comes to online retail, the terms “fulfillment center” and “warehouse” are often used interchangeably, but there are some key differences between the two.
First and foremost, the purpose of a warehouse is to store inventory, while the purpose of a fulfillment center is to store and process inventory for shipping to customers. In other words, a warehouse is primarily used for storage, while a fulfillment center is used for both storage and order fulfillment.
In a warehouse, inventory is typically stored in large quantities and is not easily accessible for picking and packing individual orders. In contrast, a fulfillment center is designed with order fulfillment in mind, and inventory is organized and stored in a way that makes it easy to pick and pack individual orders quickly and efficiently.
Another significant difference between fulfillment centers and warehouses is the level of automation. Fulfillment centers tend to be more automated than warehouses, with the use of technology such as conveyor belts, sorting systems, and robots to facilitate order fulfillment. Warehouses, on the other hand, tend to rely more on manual labor.
The Fulfillment Process
A shipping fulfillment center performs a range of activities that a warehouse typically does not, including managing the entire fulfillment process for businesses. The fulfillment process is a critical aspect of the e-commerce supply chain and includes several distinct stages. Here are the stages involved in the fulfillment process:
- Receiving Orders: When a customer places an order through an e-commerce platform, the order is forwarded to the fulfillment center for processing.
- Order Processing: Once the fulfillment center receives an order, the details are verified, product availability is checked, and payment is authorized to ensure that the order can be fulfilled.
- Order Picking: Following the processing stage, the fulfillment center picks the products from storage and prepares them for shipping.
- Packing and Labeling: After selecting the products, they are packed, and shipping labels are affixed. The packing process guarantees that the products are secure during transport and arrive at the customer’s destination in good condition.
- Shipping: After packing is completed, the products are dispatched to the customer using different shipping methods. The fulfillment center is responsible for ensuring that the products are delivered on time and in excellent condition.
If you’re astute, you’ll have noticed that there is some overlap between the functions of fulfillment centers and those of warehouses, and you’d be correct. This is because, essentially, while all fulfillment centers are warehouses, not every warehouse is a fulfillment center.
Additionally, you might encounter another term used interchangeably with a fulfillment center – a fulfillment facility.
Fulfillment Companies (3PL)
In contrast, a fulfillment company is a 3PL (third-party logistics) provider that specializes in providing fulfillment services. These companies are what you call the business entities that run fulfillment centers and, depending on the business strategy of the fulfillment company in charge, they may invest more heavily in certain functions over others. For example, there are fulfillment centers that focus on quickly responding to orders, whereas others offer specialized storage options.
How Does a Fulfillment Center Operate?
Now that you have a clear comprehension of what a fulfillment center entails, let’s explore its operational procedures. When a business collaborates with a fulfillment distribution center, it typically sends its goods to the center for storage. The fulfillment center then proceeds to receive orders from the business’s e-commerce platform and initiate the fulfillment process.
Initially, the center chooses the products from storage and readies them for shipping by packaging and incorporating any required labeling or branding. The products are subsequently shipped to customers through a range of shipping methods.
Fulfillment centers utilize different shipping methods to deliver products to customers and clients and will usually offer several shipping choices to fulfill specific requirements.
Some popular shipping methods include:
- Standard Shipping: This is the most cost-effective option, typically taking 3-7 business days for delivery.
- Expedited Shipping: This method is quicker than standard shipping, with delivery times ranging from 1-3 business days. However, it’s usually more expensive.
- Next-Day Shipping: This is the fastest option, delivering products the next business day after shipment. However, it is also the most expensive.
- International Shipping: This method is used for shipping products to customers outside of the country where the fulfillment center is located. The delivery time for international shipping can vary based on the destination country and customs clearance.
- Freight Shipping: This option is utilized for shipping large and heavy items that cannot be shipped through typical parcel carriers. Freight shipping usually takes longer and is more costly than other options.
What Are the Differences Between Long-term vs. Short-term Storage?
In the realm of shipping fulfillment center operations, one crucial aspect to consider is the contrast between long-term and short-term storage.
Long-Term Storage Uses
Long-term storage is generally used for products that are seasonal in nature or not expected to sell rapidly. Some examples of these types of products include
- Winter coats
- Holiday decorations
- Gardening tools
- Camping gear
- Halloween costumes
- Christmas ornaments
These products may have low demand for the majority of the year, with demand sharply increasing during a particular season or holiday. As such, long-term storage is a practical option for these products.
Short-Term Storage Uses
Conversely, short-term storage is utilized for products that are anticipated to sell quickly and need to be readily accessible for fulfillment. Some examples of these types of products include:
- Popular electronics
- Newly released books or movies
- Trending fashion items
- Limited edition collectibles
- Perishable goods, such as fresh food or flowers
As the demand for these products is typically high, short-term storage is a practical solution to ensure that they are quickly available for the fulfillment process.
See Also:
3PL: Benefits, Services, & Technological Development
Outsourcing fulfillment to a 3PL provider can benefit businesses in terms of saving time and money. By utilizing a local fulfillment center, businesses are relieved of the responsibility of managing their own warehouse or hiring personnel to handle order fulfillment. This can save time and resources that can be directed toward other aspects of the business.
Another benefit of utilizing a 3PL fulfillment distribution center is the ability to provide fast and reliable shipping to customers. Fulfillment centers have access to various shipping carriers and can often negotiate better rates than individual businesses. This enables businesses to offer competitive shipping rates, including expedited shipping options such as one- or two-day delivery.
E-commerce Fulfillment Services
E-commerce fulfillment services are a specialized type of 3PL service that primarily focuses on fulfilling orders for e-commerce businesses, such as Shopify or Amazon. Unlike traditional fulfillment services, which may cater to a variety of industries, e-commerce fulfillment services are specifically designed to support the unique needs of online businesses enabling them to streamline their operations and focus on other areas. E-commerce fulfillment services on offer typically cover:
- Warehousing: 3PLs offer businesses storage facilities and manage inventory levels to ensure that the right products are in stock when needed.
- Order Processing: When an order is received, 3PLs handle the entire order processing, including verifying the order details, checking product availability, and authorizing payment.
- Pick and Pack: After processing the order, 3PLs pick the products from storage and pack them for shipping, applying shipping labels, and managing necessary branding or labeling requirements.
- Shipping: 3PLs provide various shipping options, including standard, expedited, and international shipping. They work with multiple carriers to negotiate competitive shipping rates and ensure on-time product delivery.
- Returns Management: 3PLs manage the returns process, including handling product returns, issuing refunds or exchanges, and restocking returned products.
- Inventory Management: 3PLs employ advanced inventory management systems to track product inventory levels, alert businesses when stock levels are low, and manage product reordering.
- Kitting and Assembly: Some 3PLs offer kitting and assembly services, which bundle products together to create custom product bundles or kits.
- Quality Control: 3PLs implement strict quality control measures to ensure that products are accurately picked, packed, and shipped to customers.
- Customer Support: Many 3PLs offer customer support services, including phone and email support, to assist businesses with order-related inquiries and issues.
Automation & The Fulfillment Process
Automating the fulfillment process is a useful way to streamline operations further. Fulfillment centers can leverage various automation technologies, such as conveyor belts and robotic picking systems, to expedite the fulfillment process and minimize errors. 3PL fulfillment companies are continually exploring new methods to automate and streamline warehouse operations. Here are some examples of automation technologies that are commonly used in fulfillment centers:
- Automated Storage and Retrieval Systems (ASRS): Robots that transport products from storage to picking areas, significantly reducing the time required to retrieve products.
- Automated Guided Vehicles (AGVs): Equipped with sensors and navigation technology, these vehicles autonomously transport products throughout the warehouse.
- Robotics: Robotic arms and grippers are utilized for picking, packing, and sorting products, increasing speed and accuracy.
- Conveyor/Sortation Systems: Conveyors, scanners, and other technology transport products between different areas of the warehouse, reducing the need for manual labor.
- Pick-to-Light Systems: Light indicators are used to guide warehouse personnel to the precise location of the product, decreasing the time required to pick products.
- Automated Packaging Systems: These systems automatically package and label products, reducing the time and labor required to prepare products for shipping.
- Warehouse Management Systems (WMS): WMS software provides real-time inventory data and helps manage warehouse operations, increasing efficiency and reducing errors.
- Internet of Things (IoT) Sensors: IoT sensors are placed throughout the warehouse to track product movement, monitor inventory levels, and provide real-time data on warehouse operations.
- Augmented Reality (AR) and Virtual Reality (VR): AR and VR can be used to train warehouse personnel, simulate warehouse operations, and improve order-picking accuracy.
What Does a 3PL Fulfillment Center Do?
In summary, 3PL fulfillment companies handle the entire fulfillment process for businesses, from product storage to shipping. This allows businesses to concentrate on other facets of their operations while the fulfillment center handles everything else.
How Do 3PL Fulfillment Centers Work?
When a business collaborates with a 3PL fulfillment company, they generally send their products to the center for storage. The center then accepts orders from the business’s e-commerce platform and commences the fulfillment process. This process involves picking the products from storage, packaging them, and shipping them to customers. Additionally, fulfillment centers can manage returns and offer businesses real-time inventory tracking and management.
Fulfillment Warehouses
E-commerce fulfillment warehouses are primarily used for product storage but with a layout and infrastructure that is specifically designed to optimize the efficiency and speed of the fulfillment process; this may include conveyor systems, automated picking and packing technology, and other tools and equipment that streamline the process and reduce the risk of errors.
However, businesses are responsible for handling the order processing, picking, packing, and shipping. While both fulfillment centers and warehouses provide businesses with storage space, a fulfillment center offers more comprehensive services.
As such, 3PL businesses operating out of e-commerce fulfillment warehouses are more suitable options for clients that have already established their own fulfillment process and are primarily looking for storage solutions.
Frequently Asked Questions (FAQs)
Can a Fulfillment Center Do One- or Two-Day Delivery?
Yes. One of the advantages of partnering with a fulfillment center is that they have access to a range of shipping carriers and can often negotiate better rates than individual businesses. This enables them to offer a variety of shipping options, including expedited shipping options like one- or two-day delivery.
Meeting one- or two-day delivery demands can be challenging for individual businesses, especially for those that do not have their own fulfillment infrastructure in place. Small businesses often face challenges in meeting fast delivery demands due to limited resources, time constraints, shipping costs, inaccurate inventory management, and limited shipping options.
These businesses may not have the necessary technology and equipment to streamline their fulfillment process and achieve faster delivery times. In addition, without a dedicated fulfillment team, they may struggle to process orders quickly, especially during peak periods.
Expedited shipping options can also be costly, and businesses may not have the negotiating power to secure favorable rates. Furthermore, inaccurate inventory management can lead to delays and dissatisfied customers, and limited access to shipping carriers can make it difficult to offer expedited shipping options.
Fulfillment solutions provided by 3PL businesses help small and individual businesses overcome these challenges. By offering faster shipping options, businesses can improve customer satisfaction and increase the likelihood of repeat business.
What is a Good Price for Fulfillment Solutions?
In terms of pricing, there are many factors to consider when evaluating the cost of using a fulfillment center. The size of the business and the level of services required are important factors that can impact pricing. Typically, fulfillment centers charge a fee for storing, picking, packing, and shipping goods. The cost of these services can vary depending on the volume of orders and the complexity of the fulfillment process.
It’s important to note that while the cost of using a shipping fulfillment center may seem high at first glance, it can often save businesses time and money in the long run. By outsourcing fulfillment to a 3PL provider, businesses can avoid the costs associated with managing their own warehouse, hiring and training staff, and investing in the necessary technology and equipment.
When evaluating pricing from multiple fulfillment providers, it’s important to look beyond the cost per service and consider the value and quality of the services provided. Ultimately, the right fulfillment center will offer competitive pricing and high-quality services that meet the specific needs of your business.
Final Thoughts
To sum up, partnering with a fulfillment company can help businesses scale more efficiently by allowing them to focus on core operations and marketing efforts while leaving the fulfillment process to the experts. Fulfillment companies also offer additional services such as kitting, bundling, and customized packaging, which can help businesses differentiate themselves from their competitors.
However, it’s important for businesses to choose the right fulfillment company that aligns with their specific needs and goals. Businesses should research and compare different fulfillment companies based on factors such as pricing, services offered, technology and software integrations, and reputation. By choosing the right fulfillment partner, businesses can optimize their fulfillment process, improve customer satisfaction, and ultimately grow their business.
Looking to level up your business with intelligent funding and 3PL company services? PIRS Capital has you covered! With financial solutions and quality customer service, we’re committed to helping your business grow. Our experienced team takes the time to understand your industry, needs, and opportunities to provide tailored funding solutions.
Ready to achieve your business goals with financing solutions that work for you? Contact PIRS Capital today!
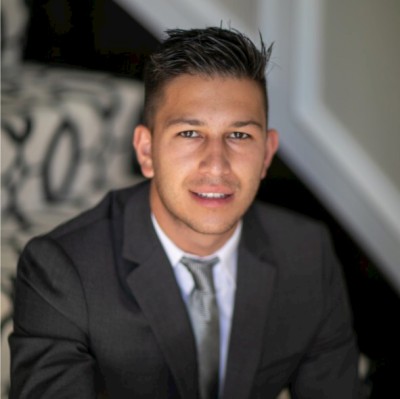
I work with companies that sell products on platforms such as Amazon, Shopify, Walmart, Ebay, Etsy, etc. I understand that every business is unique and thats why I form genuine relationships with owners so I can help them reach their goals and find success through our working capital solutions.